Xi'an’s Glodon R&D Building Project
Xi’an, China
-
Project Type & Description: R&D Building
-
Gross Floor Area: 66,278 m2 frame shear wall structure, with 3 floors underground, and 12 floors above ground
-
Glodon Products Involved: BIM5D
Sustainable Glodon(Xi'an) R&D Building Adopted Digital Twin
Considering sustainability and targets China has, Glodon decided its latest building investment to meet this target by utilizing the Digital Building Platform. Xi'an’s R&D Building (Image 1) uses this approach through the lifecycle (from design to operation) by using an integrated and innovative solution based on Digital Twin paradigm. Consequently, besides meeting the green (COP26 and Sustainability) targets, the advanced use of Digital Twin (DT) with AI over the Digital Building Platform allowed the BoD to understand how to better manage the company’s assets (now and future). Even the building is still under construction real-time DT information shows significant results ensuring goals are achieved.
Image 1: Facade of Glodon’s Xian R&D Building as extracted from the Digital Twin Model
Challenges
Recently, Digital Twin (DT) is gaining more attention in the AEC industry due to its potential values and promising benefits. However, there are still some challenges we need to keep in mind about DT. First of all, there are only a few software or solutions available in the market. This indicates DT is not an option for everyone, especially for SMEs.
Secondly, data is the key to DT. Data disconnection of each stage during the entire lifecycle weakens DT's values. For example, the operation and maintenance stages are the value point of DT. Lack of accurate design and construction data, modelers need to rebuild models by using technologies such as point cloud which is expensive and time-consuming.
Last but not at least, DT was mapped to our business model. Therefore, we became more critical of how DT was applied. On this basis, it was important to show the added value to both stakeholders and the company’s shareholders ensuring that they have a very good and thorough understanding of how the building is going to be constructed and later operated. So, we learn by not being able to demonstrate evidence to both stakeholders and shareholders was not possible to show them the added value of DT towards better construction and asset management. So, by standardizing the DT process as part of the project lifecycle it helped to eliminate these challenges (risks) and understand the opportunities of DT application
Projects’ Outcomes
Glodon (Xi'an) Digital Building R&D Mansion Tower: The building has a total construction area of 66,278?m2, a frame shear wall structure, 3 floors underground, and 12 floors above ground. The Project started on September 16, 2019, and its structure was completed on May 25th in 2021.
The digital building platform is also a production line based on the digital twin, which drives the physical production line for synchronous operation and collaborative management (image 2). Based on the project control unit real-time scheduling, production scheduling, logistics scheduling, and construction scheduling are conducted between the factory and the site through this platform, forming integrated management.
With the help of BIM technology, integrated with the on-site IoT and AI technology, the real-time twinning of the model data and real data was applied. The whole process was data-driven, and the on-site industrial construction was initially designed to ensure the quality of process standardization. The data-driven lean construction was also implemented.
Through the digital building platform, based on the smallest process management unit- five elements of lean management affect the success of the project: ?progress, cost, quality, safety, and environment. In the office, the digitization was conducted in terms of process-level in-depth design, scheduling, resource procurement and supply, and other business so that design, scheduling, and procurement are in place. Digital building platform helps digitize the office, construction site and working surface, and enables them online. Driving the allocation of relevant resources through the business needs on the construction site ensuring the supply of labor, material and machine, and the operation on the construction site in place.?
Image 2: Lean Construction of Digital Twin
Through, the dynamic optimization?of progress, timely payment of costs, guarantee of quality and prevention of accident were applied too. At present, 80% of the process tasks have clear operating standards, and the building’s quality standards have been upgraded.
Through planning and scheduling?to the last level and task execution to the minimum process, the whole schedule management process has been dynamically optimized. In addition, the labor team and suppliers were paid on time according to the process tasks (in contrast to traditional payment method payments were based according to the contract progress measurement).
Relying on the data driving force of the digital building platform, AI learning, graphics technology, cloud computing, etc. were innovatively applied to develop an increased intelligent bill of quantities (image 3). With the help of big data, the designer, developer, contractor, and building materials suppliers were connected to offer data services such as material selection and pricing throughout the whole life cycle.
Image 3: Industrial Lean Construction Scenario Based on Digital Twin
Through evaluation, it was also built an industrial supply chain service-based platform?to provide new ideas and models for the transformation and upgrade of supply chain finance. Moreover, by using the digital building platform, Xi'an Building has been "built twice". In fact, two "buildings" are delivered (virtual and physical buildings).
For the virtual building digital models?will be delivered through digital virtual construction such as collaborative design, virtual production, virtual construction, and virtual operation and maintenance. Then, the industrial intelligent lean construction that integrates both digital production line and physical production line will help towards the delivery of high industrial quality of the physical building.
Summary
Based on cutting-edge science and technology, the digital building is implemented to offer industrial quality and human-oriented healthy buildings, and thus fully meet people's individual needs. The intelligent building can implement a comprehensive analysis through deep cognition, intelligent interaction, and self-evolution. The cloud among other services can also quickly compute based on the real data from various sensors in the building. Consequently, the building is becoming a "living body", analyzing the indoor environment such as temperature, humidity, wind speed but also monitoring health status, and providing other humanized services.
Digital technologies run into and merge with the building industry, having a great impact on its digital transformation. The development paradigm of the digital building platform that is fully DT supported converts the building industry into a dynamic ecosystem (image 4) that offers better cooperation and thus a value chain supply is developed.
Image 4: Digital Twin Application in Xi’an R&D Building
The traditional building industry must be deconstructed from all elements, processes, and stakeholders, and reconstructed through digitalization, online system, and intelligence to build the new design, new construction, and new O&M.
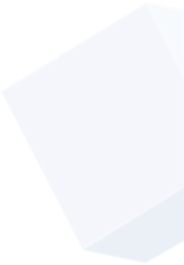